One of the giants of the UK car industry Sir Herbert Austin almost a century ago stated that ‘ Any electrical apparatus is usually regarded by the average person with fear or as somewhat of a mystery.
Sir Herbert knew what he was talking about as even today the average unqualified person remains reluctant to tackle a vehicle's electrical systems.
Wires and fuses along with the switches and connectors that connect them go to make up a wiring harness commonly known as "looms".
Without an efficient wiring harness (otherwise known as the loom )installed, any renovation project will be doomed to failure.
That's the reason why someone with an intensive knowledge of auto electrics must be involved in the repairs and renovation of a classic car's wiring system.
Many of the problems that are liable to crop in a car's electric system renovations will be due to a combination of simple system failures, usually caused by a loose spade, a broken wire or by a connector furring up .
To bring a vehicle's wiring up to scratch, it is essential to understand the basic procedures involved in maintaining the main arteries of the car's wiring system.
First and foremost is the wiring whose function is to connect the vehicle's various components. Collectively a vehicle's wiring system is known as its *loom' or 'harness'.
For the good or the bad, UK and European cars of the Fifties and Sixties had an electric system that, at least concerning today's vehicles, was very simple with much fewer wires.
Most Fifties and Sixties classics run their electrical system through a single fuse board, usually mounted on or through the bulkhead (firewall).
Typically, the type of wiring in classic cars comprises strands of copper and steel, enclosed in a non-conductive coating such as PVC plastic or rubber and cotton.
This type of wiring was known for its longevity, unlike the earlier rubber/ cotton type insulators that more than likely will likely have perished in a classic previous to renovation.

Even the most inexperienced electrician will be well aware that the dimensions of each cable combined with the number of strands that make it up will be related to the amount of current that it needs to carry.
Failure to do so will place the newly renovated car at risk of fire or electrical damage.
Over the years, car manufacturers invested considerable time and effort in bringing in standards for colour coding.
While the standards they set were commendable, over the years, for unexplained reasons, these standard colour codes were not adhered to during repairs to the wiring system, causing tremendous confusion.
To return a semblance of order to the renovation car's wiring system, it is very worthwhile to ensure that an original manufacturer's wiring diagram is on hand, preferably relating to the year the vehicle was produced.
The first step before a single wire has been crimped is to carry out a proper assessment of the car's wiring system.,
The first thing that the auto-electrician should look for is signs of stress fracturing and metal fatigue in the car's wiring, a widespread phenomenon in older vehicles.
Over the years, most metals will become brittle or 'work-hardened if repeatedly bent one way and then the other way.
An experienced electrician will save some time focusing on areas where a cable section is rigidly fixed. Once discovered, simply shortening the wire should solve the problem.

A vehicle's wiring system can be especially vulnerable where any connections have had to be made. The auto-electrician should carefully scan the vehicle's loom to ensure that there are no breaks or joins in the wiring.
If breaks are found, all the joints should be soldered.
Those without experience or confidence to risk soldiering a joint can compromise by fitting a push-fit connector.
Push-fit connectors can be attached to their respective wires not only by soldering and also crimping or held together by friction.
The advantage of most push-fit connectors is that they are self-cleaning, meaning that by simply pulling the joint apart and then pushing it together, any build-up of oxide will be removed.
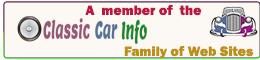
For an emergency field repair, it is always good to carry some shrink wrap in the car. Shrinkwrap is a handy method of sealing and insulating an electrical joint but only as a temporary measure.
The shrink wrap is placed around the newly formed joint and heated. The wrap then shrinks and creates a quick but effective seal.
Another stop-gap that's worth keeping in the car for various reasons is Insulating tape, traditionally among the all-time great problem solvers. No toolbox should not be regarded as complete with at least one roll that can be rapidly called into action to wrap all manner of electrical joints and loose ends.